Innovators in medical device coatings: inside Formacoat’s unique R&D team
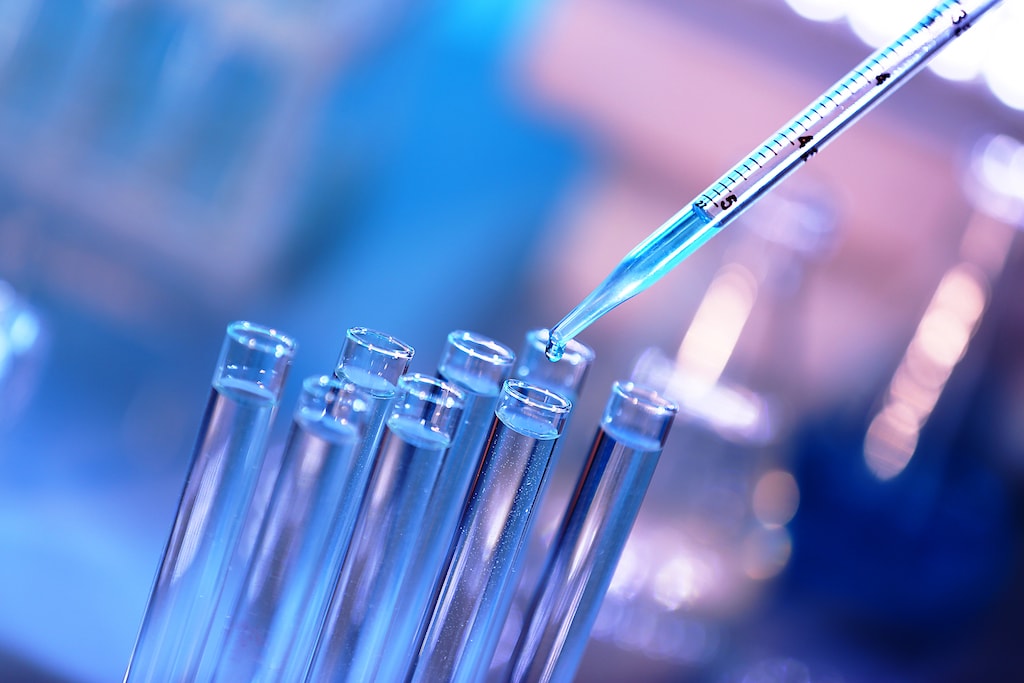
The solution for medical device coatings is not always straightforward, but the best R&D teams can usually find one. Formacoat has built a reputation for being able to provide coatings for the trickiest types of applications thanks to its highly innovative R&D team willing to take on any challenge. We learn more about the team and their processes, from first contact to final polish.
With growing numbers of medical devices being designed to address ever more specific needs, there is a possibility that the optimum coating required has not yet been invented. Sometimes, being unable to find the right coating can put a stop to medical device development, depriving patients of potentially life-changing solutions.
To ensure that innovation continues, and the patients benefit, new coating application methods and custom coating modifications may need to be created: Enter Formacoat’s innovative R&D team.
When it comes to R&D, Formacoat has carved a niche of its own, rapidly delivering specialist solutions that meet precise needs. R&D at the family-owned business spans from refining coating formulation to rapid development of the tooling and prototyping necessary to coat things at scale.
“I would describe R&D operations here as a unique niche,” says Jesse Manley, innovative research and development engineer at Formacoat. “In the coating application world, a lot of companies either make coatings, or they are like a machine shop, or they generally apply coatings. We have many tools here at our disposal to be pretty nimble.
“We accommodate all sorts of strange problems, whether they be chemical-related or physical shape-related. Medical devices are definitely starting to get smaller and more complicated.
“There are a lot of demands on all of those facets where we do R&D. So, it’s variable. It’s very quick-paced and there tend to be multiple things that aren’t known. We have to figure out a lot of stuff.”
Alongside the diversity of services, speed is another thing that sets Formacoat apart from other coatings providers in the industry, which significantly accelerates the timeline from concept to cash flow.
“In bigger corporations, your projects are measured in years. Here, our projects are measured in weeks,” adds Manley.
“In a big company, you’ll have more focused teams, like multidisciplinary teams. Here, it’s kind of you. And you have to rapidly go through the problem-solving. If you can’t, you’re gathering your peers and trying to work through problems pretty quickly. Often, we talk about how fast can we do it? How effective can we do it? We perform a lot of base work, but we’re always trying to tie it to scientific principles.”
Finding the optimum medical device coating through R&D
The R&D process starts with understanding the customer’s requirements and the function their device will provide. Findings within specific projects increase learnings and understanding, which can be applied to other areas.
“The main thing for us when we start approaching a new coating project is communication: what does the customer want and why? (Note: this is the trademarked “Formacoat Formula). Do they want it to be lubricious or hydrophobic? What’s their end goal for the device?” says Matt Follmer, R&D engineer at Formacoat. “From there, we take that information, as well as what we have in-house such as internal projects we’re working on that might fit into that. We work towards getting that product to their performance goal.”
Collaboration is central to R&D at Formacoat. The team bounce ideas off each other to figure out the best approach for a project. And while the R&D process at the Minnesota-based business is fast, it is also thorough.
“When we get into these projects that we’re trying to figure out how to do we all come together as a group and spitball ideas,” adds Kyle Szilagyi, Formacoat R&D engineer. “Multiple minds are better than one trying to figure out how to solve a problem or project. We tend to sit down and put our heads together.”
The concept development process is robust, with ideas subject to considerable scrutiny to determine whether there are any flaws or potential weak spots. This level of constructive criticism is integral to developing new ideas.
“It’s like a coliseum of ideas,” explains Manley. “If your idea is surviving the coliseum, we should go with it, or at least it’s worth a good try. But if it’s too weak to survive a few questions, then let’s not bother.
“You need kind of a safe place to be critical of each other’s work, where you trust that everyone’s input is for the betterment of everybody.”
A culture for coatings innovations
To an outsider or even an experienced R&D specialist, the operations environment at Formacoat is unlikely to be similar to anywhere they have ever worked. Yet the proof of the R&D team’s effectiveness is how the company can provide more than 90 varieties of coatings from 45 different suppliers. One can simply not just be a Chemical Engineer. Formacoat calls on their employees to wear many different hats and call on every bit of the skill and guile to help solve the variety of problems on any given day. And for the newest member of the R&D team, Kyle Szilagyi, there has been a lot to learn.
“It was a struggle at the beginning because I came in with just a chemistry degree. I didn’t have an engineering background,” he says.
“But they had faith in me to be able to get projects done and think outside the box. It was a challenge at first, but I’m getting better and the guys have been super helpful every step of the way. I feel like I’m settling in pretty well, and the culture here is just great.”
Szilagyi agrees that working at Formacoat gives him a chance to use his creativity and initiative more than in places he has previously worked.
“I feel like I accomplished something myself, or it’s these projects that I’ll be working on slowly with some input from other guys,” he adds. “And just to feel like I’m putting out something that a customer wants and is to their specifications, it’s a big sense of accomplishment.”